By Karen Knapstein
Cold is the absence of heat. In a metal building where the air is either heated or cooled, heat is readily transferred through the metal, which, as you well know, is the most-used exterior cladding on post-frame buildings.
Insulating a structure reduces heat transfer. It prevents a building from acting like an oven when it’s hot outside, and it reduces the energy needed to heat the building when it’s cold outside. No matter how airtight the building envelope, heat will still transfer through the building materials. Insulation helps keep heat where it’s wanted.
Heat Gain/Loss
There are three modes of heat transfer: conduction, convection, and radiation. Conduction is direct heat flow through matter. It results from actual physical contact of one part of a body with another part of the same body, or of one body with another. For example, aluminum is a strong, light, and stable material (i.e. it doesn’t warp) that is easy to work with. All these characteristics make it a great choice as a window-framing material. However, aluminum transfers heat very well. This means, without a thermal break, an aluminum-framed window would do an excellent job conducting the heat from the inside to the outside of a heated building. The thermal break separates the inside aluminum from the exterior aluminum so the heat isn’t conducted through the frame.
Convection is the transfer of heat within a gas or liquid, caused by the actual flow of material. In building spaces, natural convection heat flow is mostly upward and somewhat sideways. For example, a floor warmed with an in-floor radiant heating system loses heat by convection to the cooler air in contact with it. The sideways motion comes from cooler, heavier air rushing in from the side (and perhaps below, depending on the structure) to replace it.
Radiation is the transmission of infrared rays through space. Every material for which the temperature is above absolute zero emits infrared radiation. All objects radiate infrared rays from their surfaces in a straight line in all directions until they are reflected or absorbed by another object. Even though the air is cool on a cool day, sunlight still feels warm because of the infrared radiation.
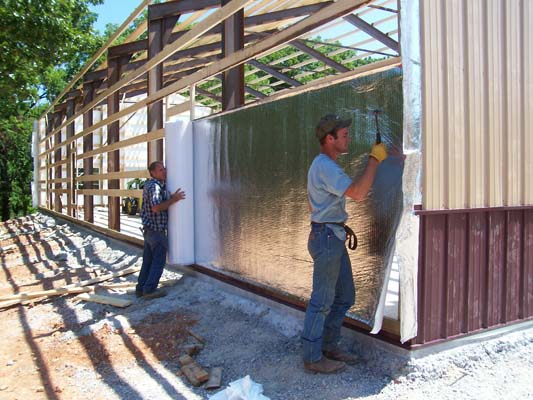
Thermal Bridging
A thermal bridge (aka cold bridge, heat bridge, or thermal bypass) is an area that has higher thermal conductivity than the surrounding materials. This creates a path of least resistance for heat transfer from the warmer to the cooler materials. Metal is an excellent thermal bridge. Other thermal bridges in post-frame buildings include, but are not limited to, wood-to-wood and wood-to-metal connections, as well as the contact between the ground and concrete. Thermal bridging is prevented with barriers and insulation. A continuous insulation barrier between the purlins and roof panels, between the girts and wall panels, and beneath the concrete floor create effective thermal breaks, which significantly slow or stop heat transfer.
Fiberglass
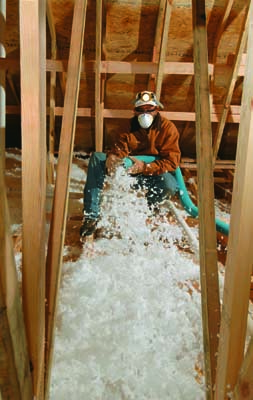
Because of its low cost and ease of installation, one of the most commonly used insulation material is fiberglass. When asked how fiberglass insulation works to mitigate heat transfer, Ted Winslow, Product Manager Building Science, Systems & Technical Marketing at CertainTeed, explained, “Fiberglass insulation is essentially to slow the heat transfer through an assembly. This is because glass chemistry and physical construction of the fibers work together to create small pockets of air that reduce conduction and thermal radiation through the cavity. Since heat travels from the warmer area to the cooler area, the fiberglass insulation can slow this process down, which is called its resistance to heat flow. This is more commonly known as the insulation’s R-value, and it can be used to compare the performance of different types of insulation with the higher R-value indicating the higher resistance to heat transfer.”
Fiberglass insulation is typically best installed before installing the finishing surfaces (e.g., drywall) and after all air sealing needs have been addressed. “It is important to note that proper air sealing is key to optimizing the performance of all insulating materials,” said Winslow. “The key thing to understand when it comes to installing fiberglass insulation is to pay attention to details and have a comprehensive understanding of the impact of compression,” he continued. “When properly installed, fiberglass insulation is a great low-cost insulation material; however, when it becomes compressed, it can reduce the thermal performance of the material.”
A vapor barrier is used to damp proof the wall, floor, ceiling, or roof assembly to prevent condensation within the cavity. Winslow explains, “Vapor retarders are driven by state and local building code requirements, based on climate zone needs. Buildings located in Climate Zones 4c and above will typically require a vapor
retarder be installed. Vapor retarders are a key component to installing many insulation systems because they provide a control layer that prevents moisture transfer through the insulation—helping to optimize its performance and to avoid condensation within the wall cavity. If not managed with a vapor retarder, this moisture can also lead to a variety of moisture-related issues (e.g., mold, rot, etc.) over time.”
Bubbles and Foil
Reflective insulation helps control unwanted heat transfer and prevents condensation. Products such as Covertech Flexible Packaging’s rFoil®, Plyco Corporation’s Ply-Foil and MWI Components’ Infinity Shield™ drastically reduce that heat gain because most aluminum insulations reflect 95% (or more) of all radiant energy that strike its air-bounded surfaces. The bubble core and metalized film provide an excellent combination of heat reflection and thickness to stop both radiation and convection heat loss/gain. As a bonus: Aluminum foil is one of the few insulating materials that is not affected by moisture, so its insulating value remains constant regardless of humidity and it’s well-suited for installation in post-frame ag buildings.

To take a closer look at one example, Covertech’s rFoil 2500 Series and 2600 Series of metal and post-frame building insulation consist of a layer of polyethylene bubble bonded to and sandwiched between a radiant barrier metalized foil and a white polyethylene sheet with washable UV-resistant facing. The 2200 Series is a layer of polyethylene bubbles bonded to and sandwiched between two radiant barrier metalized foil sheets. John Starr, Vice President/Partner at the Toronto-based company said rFoil is a “pretty simple product that solves a major problem. It provides a cost-effective, energy-efficient way to insulate a building, controlling heat gain and loss and condensation.”
“rFoil is pretty easy to work with,” Starr continued. “It’s not thick, it’s lightweight and easy to install. If it tears, it’s easy to repair.” The most common question he answers is “Which side goes up?” He said: “The foil facing side always goes towards the metal.”
Depending on the goals, NOFP’s Solex, MicroFoil and Performance Star insulations also provide the desired reflectivity and thermal barrier needed to prevent the transfer of heat, giving the owner a better environment for work, house equipment and/or livestock. “Our Barrier™under concrete insulation works great in agricultural buildings to keep the floor at a more constant and consistent temperature,” says Jason Brown, Sales Manager for Northwestern Ohio Foam Products, Inc. (NOFP).
Additionally, the importance of proper insulation in a post-frame residence cannot be understated. Brown, explains, “In residential applications, insulation becomes a major factor in providing a comfortable climate in the home. The right insulation will contribute to reducing energy consumption and will allow the building to maintain its temperature longer. Our Barrier under concrete insulation allows you to easily implement in-floor heat to keep the floors warm during the winter months. Our Solex, MicroFoil or Performance Star all provide the reflective qualities most people find important in insulating their homes.”
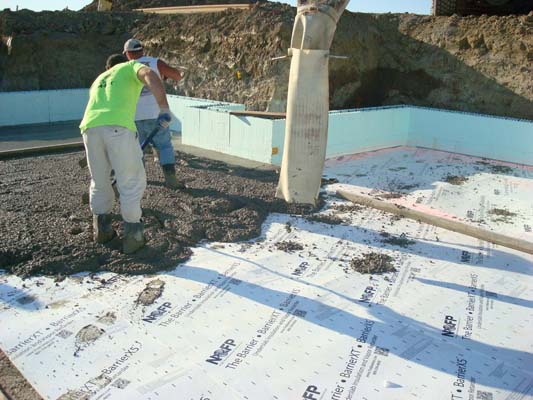
Expanded Polystyrene (EPS)
To prevent moisture migration and heat transfer through concrete, an insulator and/or vapor retarder must be installed between the ground and the concrete. Like a foam cup protects your hand from a hot beverage, expanded polystyrene foam protects concrete from moisture and prevents heat from transferring to the ground — especially when used in in-floor radiant heat applications. NOFP manufactures a family of EPS foam products to serve this purpose. The core of the Barrier™ roll products is made of flexible, recycled expanded polystyrene to provide insulating characteristics. The core has vapor retarding film laminated to both sides as well as a patented self-taping edge and overlapping flange to make the installation seam-free and to reduce thermal bridging. XBoard™ provides similar characteristics in a high-density rigid sheet format for even higher heat stopping power.
The Barrier™ under concrete insulation is a thermal block that insulates the concrete from the cold and dampness of the ground. The Barrier™ product line-up is strong, durable, and won’t collapse under the weight of the concrete. Since you can walk on it without the material breaking, installation is easier than using products that break under foot.
Conclusion
The purpose of the post-frame building and the location will, in large part, determine the insulating plan, and whether the plan includes bubble/foil, fiberglass, EPS, or another form of insulation. Brown concludes, “The main thing is there isn’t necessarily a one size fits all approach toward insulation. It’s important to consider the use of the building, climate, what direction the building faces, placement of doors and windows and what the owner is looking to accomplish before determining which insulation is right for your project.” FN