I got an email of FBN this morning and my eye was drawn to the piece on galvanic compatibility. It is something that I constantly run into controversy and mis-information about out there in the market place and often by folks who should know better. I gave it a read and offer comments here:
This article [Frame Building News, August 2021, pp. 38-39] has some good information, but in total is a bit misleading due to not expounding the complete story. (https://framebuildingnews.com/?p=1236)
It leaves one to rely 100% on the galvanic scale as the beginning, middle and end of the story. It isn’t. It may be the beginning, but far from the end in many common applications. The bottom line is that while this scale is the first thing most people grab to rely upon as a technical resource — it does not tell the whole truth and therefore can be very misleading.
The galvanic scale gives the order of electro-chemical behavior and therefore compatibility – but of the parent (or base) metals only. It does not consider metal oxide layers, and because all metals form oxides – well, that’s the rest of the story. The oxide is a different material than the parent metal that created it and often behaves as an insulator, preventing (or retarding) electron exchange (galvanic action) and NOT necessarily reflecting galvanic compatibility of the parent metals.
The galvanic scale reflects electrolytic behavior solely of the parent metal, so it only tells the whole truth when oxide layers are not involved – and that only happens when the electrolyte is very aggressive (acetic – e.g. sea water). For these reasons, it should not be relied upon as a sole information source. In fact, one could say that it only tells the complete truth when in the presence of salt spray or other chlorides.
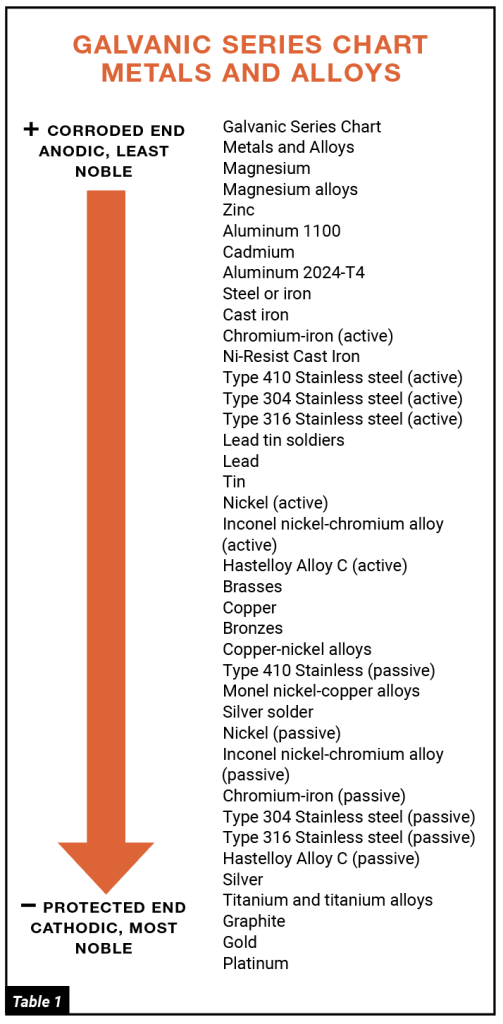
By way of example: Aluminum forms a durable oxide very rapidly in the presence of air and humidity. This is also sometimes induced by a chemical process (anodization), but it also happens naturally just with exposure. Aluminum oxide is a barrier material coating the aluminum – and it is electrically non-conductive, so electrons are impeded from passage through it from anode-to-cathode. One can use anodized or just aluminum that has oxides formed on a bare copper roof without incident in most environments. Those two metals are very distant on the scale, but compatible owing to the aluminum oxide layers.
I also read in there that dissimilar metals in direct contact always result in corrosion. Not true. Moisture is needed to establish an electrolyte. If the connection is kept dry, there is no electrolytic contact and no corrosive effect. Understanding corrosive behaviors of metals requires a much deeper dive than the galvanic scale because various metal oxides in varying environments all behave differently.
Incidentally, the Metal Construction Association publishes a Fastener Compatibility Guide that takes into consideration oxide layers and also longevity/durability considerations. It is a metal roofing industry consensus document (as opposed to what one single company or another has to say on the subject) and therefore one of the best practical resources out there.
R.M. (Rob) Haddock
Editor’s Note: To address the shortcomings of the Galvanic Action article, the MCA Fastener Compatibility Guide is published (with permission) in this edition of Frame Building News.