Using incompatible metal components results in premature corrosion
When electrochemically dissimilar metals are in contact with one another, galvanic action occurs. The direct contact creates a conductive path for electrons and ions to move from one metal to the other; the result is accelerated corrosion.
For example, consider the Statue of Liberty. Lady Liberty has a copper surface on a cast iron frame. The two metals were originally separated by an insulating material. When that insulating material failed, the result was a great deal of galvanic corrosion.
Three conditions must exist for galvanic corrosion to occur:
1 There must be two electrochemically dissimilar metals present.
2 There must be an electrically conductive path between the two metals.
3 There must be a conductive path for the metal ions to move from the more anodic metal to the more cathodic metal.
If any one of these three conditions doesn’t exist, galvanic action won’t take place.
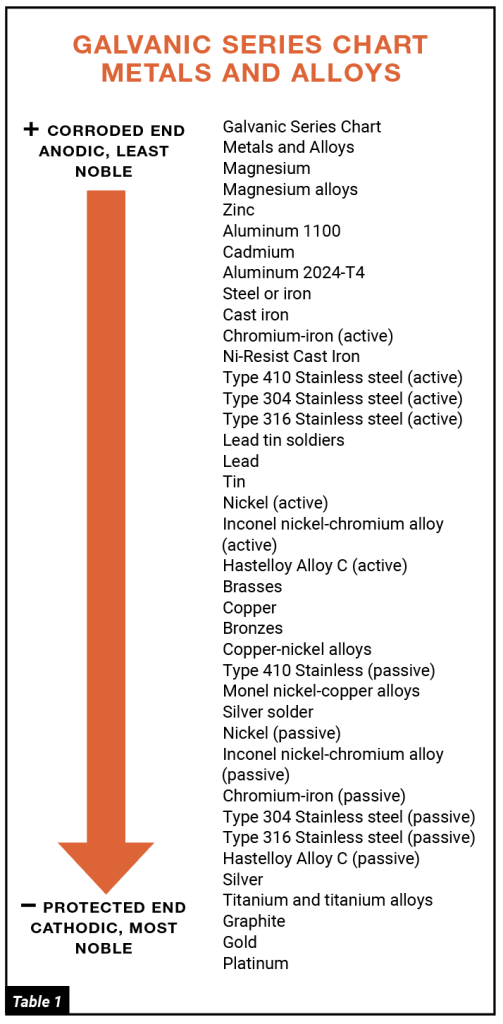
When dissimilar metals are in contact with each other in the presence of oxygen and moisture, the more noble metal (more resistant to corrosion) will corrode the less noble.
Galvanic corrosion should be a concern in the use of metal fasteners such as bolts, screws, and welds. According to an article in Preservation Science, “Because fasteners have a much smaller surface area than the materials they fasten, fasteners that take on the role of the anode will be at risk of rapid corrosion and thus should be avoided. For example, zinc-coated fasteners should only be used to connect steel coated with aluminum, zinc, and Galvalume, as these are very close on the Galvanic Series and are not generally at risk of corrosion when placed together. On the other hand, zinc-coated or aluminum-coated fasteners should not be used to attach copper or stainless-steel panels.”
Andrew Mullen, President of Direct Metals, Inc., advised, “It is important to understand the differences between metal alloys and how bare dissimilar metals in certain environmental conditions can have serious reactions that promote premature corrosion and degradation.”
To minimize the risk of galvanic corrosion occurring in fasteners, the surface metal on the fastener should be matched with the surface metal it will fasten. The most desired combination is to have a large anode with a small cathode; in other words, fasteners such as bolts and screws should be made of the metal less likely to corrode, or the more cathodic.
In the galvanic table shown (Table 1), the closer the metals are to one another on the list, the less likely they are to react to one another and experience galvanic corrosion.
If it’s not possible to avoid using dissimilar metals, coatings play a critical role in eliminating the risk of galvanic action. A non-conductive coating acts as a barrier, removing the connection between them. Common coating practices that prevent galvanic corrosion include, but are not limited to, zinc plating, galvanizing, and powder coating.
John Sheridan, owner of Sheridan Metal Resources, teaches as part of his training course: “Aluminum has a similar protective coating as zinc, eliminating risk of corrosion. Galvanized steel is coated with a fine film of zinc, so this zinc-zinc contact poses no threats. Copper and zinc don’t play nicely together. Copper runoff will stain the zinc. Steel that is non-galvanized should also be avoided, as the similar electron transfers between the metals will result in corrosion and deterioration. In addition, zinc is not compatible with oak, chestnut, red or white cedar, Douglas fir, and any woods with a pH less than 5.”
There is a good chance you already knew from experience that some fasteners react badly to certain materials. Now you know why. Remember: Your supplier will be happy to help you select the appropriate fastener for whatever materials you’re working with.
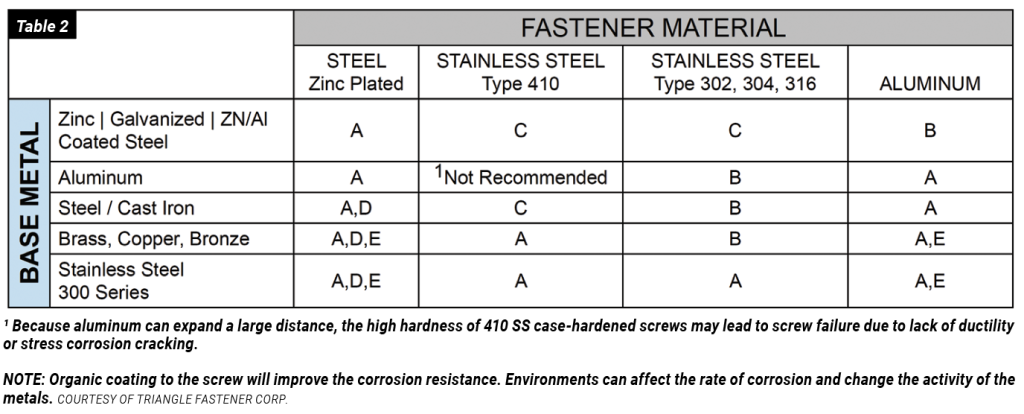
Preservative-Treated Lumber Applications
By Triangle Fastener Corporation
ACQ, Penta, CA or CBA preservative-treated lumber can be incompatible with certain types of fasteners. In those cases where any type of metal roof or wall cladding materials are being attached to preservative treated lumber, the following fasteners are not compatible: zinc plated screws, zinc-alloy headed screws, stainless capped screws, aluminum, copper and copper alloy.
When attaching metal panels to those types of preservative-treated lumber, a moisture barrier should be used between the lumber and the panel material. Metal panel fasteners that are compatible with preservative-treated lumber are stainless steel fasteners, or hot dip galvanized nails manufactured to ASTM A153 class D or heavier.
Other types of fasteners coated with proprietary anti-corrosive technologies are also available for use with preservative-treated lumber. In addition, zinc-plated screws can be used in CCA and MCQ pressure-treated lumber.